The breadboard design testing phase is over. I'm confident I can commit some Veroboard and a few of DIP sockets to build what will be a "Double Quadruple Half-H Driver Controller" board with TTL control and 8 outputs (+ve and gnd) that can be up to 36V and two gangs up to 2A per gang.
The inputs are 8 Activate lines and up to 4 Enables plus Vcc1 & GND and Vcc2 & Gnd.
I'll keep Vcc2 on it's own socket - don't want 36V hanging around the TTL lines, so that leaves 14 connections. Just right for a 15 pin D-Sub
SO I ordered 10 male & 10 female 3.5mm jacks.
I've got some 15 Way D-sub sockets so I got a couple of 15 Way D-sub 2 row male plugs. Hopefully I'll be able to use an old VGA cable for the wire, or else some ribbon cable.
Now I need to work out a Vero board layout
I found an online tool for designing stripboard. Annoyingly you can't save it when using Firefox which, obviously, I found out after designing my layout with it. It maybe can in Chrome, I'm not sure. It says Chrome works better so perhaps this is what was meant, I haven't tried it.
Anywhere, here's a screencap of the design with some annotations.
This is the view from the component side with the tracks superimposed through. The tool lets you do it differently but I'd already done it by the time I worked that out. The tool isn't excellent but at least it did what I needed.
The beauty of doing it with a designer is that there's something to test against before adding the components, which was fortunate because I had a couple of tracks conducting when the should have been isolated.
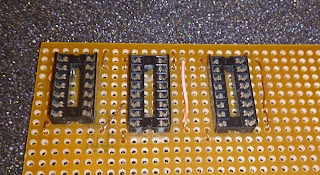
It's taken years to get this good at soldering ;) and naturally without three hands, I managed to solder the first socket in one column of holes the wrong way and the worst way, so one of the link wires is under the small socket, no big deal.